If you’ve been running WEDM for a while, you know how frustrating slow setups and alignment issues can be.
Every extra minute spent adjusting tooling is a minute your machine isn’t cutting — and when you’re using OEM System 3R components, those delays can be costly in more ways than one.
At Rapid Holding Systems, we designed the System 3R 3R-242.82HP Compatible User Kit to give you quick, precise, and repeatable positioning without the long lead times or high costs of OEM parts.
Most of our customers face the same set of frustrations in their WEDM workflows:
Slow setups, alignment issues that cause scrap and rework, and long waits (with high costs) for OEM System 3R components.
Standard setups get the job done, but they’re rarely fast. Every extra adjustment is lost production time, and when you’re relying on precision tooling, even small delays can throw off delivery schedules.
Shops running demanding EDM workflows need a faster, smarter alternative.
Why Our Customers Love Rapid Holding Systems Solutions
Our WEDM User Kits are built to solve the very challenges shops face every day. Instead of waiting weeks and paying OEM prices, our customers get:
- Full System 3R Compatibility – Seamless integration into existing setups, no hacks or workarounds needed.
- Faster Setups & Higher Productivity – Reduce downtime, cut scrap, and keep machines running.
- Proven Reliability – Precision components designed for demanding EDM environments.
- Complete Kits – Everything you need in one package, from ruler vices to levelling adapters, delivered ready to install.
With Rapid Holding Systems, shops don’t just replace parts—they gain a partner that understands the urgency, precision, and cost pressures of modern manufacturing.

The 3R-242.82HP Compatible User Kit is a drop-in replacement that integrates seamlessly with your existing System 3R interface.
No guesswork. No hacks. Just plug in, align, and cut with confidence.
Included in the kit:
- 3R-239.1 Compatible – Ruler Vice – Secure and precise clamping for square and rectangular workpieces.
- 3R-272HP Compatible – Levelling Adapter HP – Ensures perfect height alignment and repeatable setups.
- 3R-292.66HP Compatible – Magnum Holder HP – Heavy-duty holding power for larger or high-value components.
Key Benefits
50% lower cost vs. OEM System 3R components
100% guaranteed compatibility with your existing 3R setup
Fast, repeatable setups — improve productivity instantly
Built for demanding EDM environments — reliable under continuous use
Our customers report dramatic reductions in setup time, improved alignment accuracy, and the confidence of knowing that replacement parts are always available without OEM delays.
The ruler vice’s movable jaws allow you to clamp variable-length workpieces with ease. The levelling adapter ensures every setup is perfectly aligned. And the magnum holder keeps even large parts secure during long EDM runs.
Other User Kit Options from RHS
We know every shop’s needs are different — so we offer a full range of System 3R-compatible user kits to match your workflow.
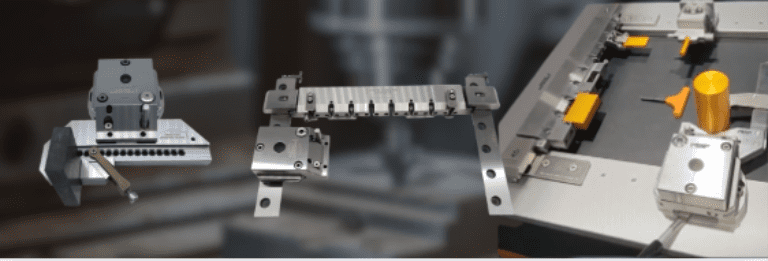
1. System 3R WEDM 3R-242HP Compatible User Kit
Includes:
- 3R-225 Compatible Reference Stop
- 3R-272HP Compatible Levelling Adapter HP
- 3R-292.3 Compatible SuperVice <100 mm
- 3R-293.3 Compatible SuperVice Ø8–90 mm
- 3R-294.3 Compatible Vice <100 mm
- 3R-914.07 Compatible Torque Wrench 7 Nm (1 pc)
- Allen Keys (3 mm & 5 mm)
Perfect for: Shops needing maximum versatility in clamping solutions for small to medium workpieces.
2. System 3R 3R-242S-3 Compatible User Kit
Includes:
- 3R-232 Compatible Levelling Adapter (1 pc)
- 3R-293.33 Compatible Universal Holder (1 pc)
- Allen Keys (3 mm & 5 mm)
Perfect for: Precision setups where universal holding is a must.
3. System 3R 3R-209-860.4 Compatible EconoRuler Kit
Includes:
- 3R-209-860 Ruler (860 mm)
- 3R-261.1 Support
- 3R-209.1 Ruler Vice, Econo
- Allen Keys (3 mm & 5 mm)
- Additional Accessories
Perfect for: Budget-conscious shops that still need reliable ruler and clamping performance.
See the full specs and order here:
System 3R 3R-242.82HP Compatible User Kit
📞 Questions? Contact us at [email protected] or call +519-999-9723.