Unlocking Productivity in a Competitive CNC Landscape
As the manufacturing industry evolves, the demand for precision and efficiency grows. Every CNC operator faces the challenge of reducing setup times, minimizing errors, and meeting tight deadlines—all while maintaining high standards of quality.
While automation has revolutionized CNC operations, investing in the right tools can provide a simpler, cost-effective solution for workshops of all sizes.
This article explores five essential CNC tools designed to enhance productivity, reduce scrap, and ensure your workshop runs at peak efficiency in 2025.
Why 2025 Is the Year to Upgrade Your CNC Tools
The new year presents an opportunity to evaluate your workflows and identify bottlenecks that slow down production. Many workshops lose hours to outdated tools and inefficient setups, resulting in missed deadlines and increased costs.
By upgrading to modern CNC tools, you can achieve:
- Faster setups.
- Consistent precision across all jobs.
- Reduced downtime and waste.
These benefits not only boost operational efficiency but also position your workshop as a leader in a competitive market.
1. Quick-Change Pallet Systems
Simplify Your Workflow, Boost Your Productivity
Lengthy setup times disrupt workflows and reduce machine utilization, especially in high-mix, low-volume jobs. Quick-change pallet systems streamline setups, allowing operators to swap workpieces quickly and maintain alignment.
Key Benefits:
- Time Savings: Reduce setup times and improve throughput.
- Precision: Maintain consistent alignment across jobs.
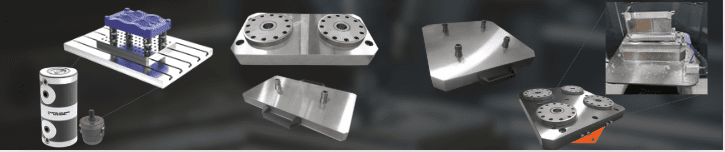
2. Self-Centering Vises
Ensure Alignment, Eliminate Scrap
Misalignment during clamping leads to wasted material, rework, and inconsistent quality—especially for irregularly shaped parts. Self-centering vises ensure perfect alignment, reducing setup time and improving machining accuracy.
Key Benefits:
- Reduced Scrap: Minimize material waste with precision clamping.
- Time Efficiency: Spend less time on manual adjustments.
- Compatibility: Works seamlessly with 3-axis and 5-axis machining setups.
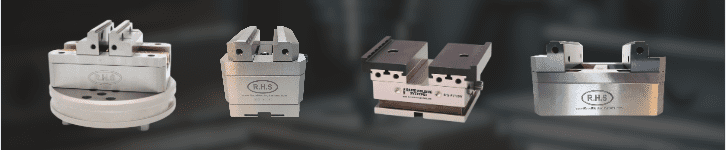
3. Zero Point Clamping Systems
Speed Meets Accuracy in Setup Changes
Frequent setup changes lead to downtime and inconsistencies in production. Zero Point clamping systems simplify the clamping process, enabling operators to fix and release workpieces in seconds with repeatable precision.
Key Benefits:
- Efficiency: Reduce setup changeover times by up to 90%.
- Accuracy: Ensure consistent results across production runs.
- Durability: Built to withstand demanding workshop environments.
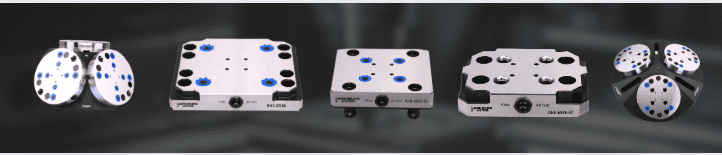
4. Multichucks
Streamline Batch Production with Versatility
Handling multiple workpieces or irregularly shaped parts in one setup can slow down operations. Multichucks enable simultaneous clamping of multiple parts, reducing downtime and maximizing efficiency.
Key Benefits:
- Increased Throughput: Process multiple parts in a single operation.
- Adaptability: Accommodates various geometries and configurations.
- Cost Efficiency: Reduce the need for additional fixtures or setups.
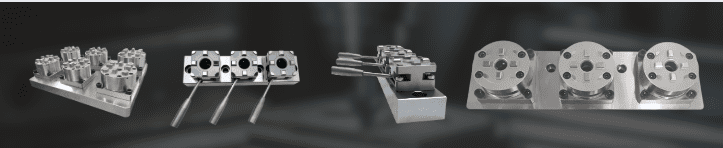
5. Wire EDM Tooling
Precision for Complex Geometries
Wire EDM operations demand stability and precision for intricate cuts, where even slight misalignments can lead to costly rework.
Wire EDM tooling provides secure, precise clamping for achieving tight tolerances in complex parts.
Key Benefits:
- Enhanced Accuracy: Maintain consistency for high-precision components.
- Material Savings: Reduce scrap with reliable clamping solutions.
- Flexibility: Compatible with various wire diameters and materials.
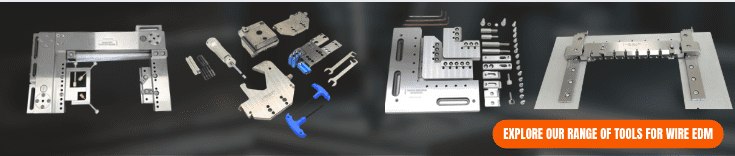
What Sets These Tools Apart?
These tools aren’t just about convenience—they’re about transforming how your workshop operates. From reducing setup times to improving precision, investing in the right equipment can save costs, enhance quality, and future-proof your operations in a fast-evolving industry.
Prepare for Success in 2025
The start of the year is the perfect time to equip your CNC workshop with tools designed to boost efficiency and precision. By integrating tools like quick-change pallet systems, self-centering vises, and multichucks, you can streamline operations and meet growing demands with confidence.
Discover how these tools can elevate your CNC workflow. Visit [Insert link] to explore our range of CNC solutions, or contact us to discuss your specific needs.